Литье в постоянные формы | Полное руководство по литью металлов
Среди многих процессов формования металлов литье в постоянные формы выделяется своей особенностью «многоразовой формы». Однако ценность этой технологии гораздо больше, чем просто срок службы формы. Она использует высокопрочные формы из стали или чугуна для достижения эффективного формования расплавленного металла различными способами заливки, такими как гравитация, низкое давление или вакуум.
По сравнению с традиционным литьем в песчаные формы литье в постоянные формы имеет больше преимуществ в точности размеров, качестве поверхности и механических свойствах; по сравнению с литьем под высоким давлением оно больше подходит для производства высококачественных отливок из алюминиевых сплавов в условиях среднего и низкого давления. От стабильности процесса до свойств материала этот метод становится идеальным балансом между точностью изготовления, затратами на обработку и массовым производством. Пожалуйста, продолжайте читать следующее подробное введение:
1. Что такое литье в постоянные формы ? Чем оно отличается от других процессов литья?
Определение Пояснение
Литье в постоянные формы — это метод литья, который использует прочные, многоразовые формы для формирования расплавленного металла в детали и компоненты. В отличие от литья в песчаные формы, которое является одноразовым, формы, используемые при литье в постоянные формы, обычно изготавливаются из стали или чугуна и могут использоваться от сотен до тысяч раз. Процесс обычно представляет собой гравитационное литье, а для улучшения эффекта заполнения также может использоваться низкое давление или вакуум .
По сравнению с литьем в песчаные формы
По сравнению с литьем в песчаные формы, самым большим преимуществом литье в постоянные формы является то, что повторно используемая металлическая форма может обеспечить более высокую точность размеров, лучшее качество поверхности и более стабильные механические свойства. Это в основном связано с хорошей теплопроводностью металлической формы и высокой скоростью охлаждения, что может способствовать формированию расплавленным металлом плотной и мелкозернистой структуры и улучшению комплексных характеристик материала.
По сравнению с литьем под давлением
Кроме того, литье в постоянные формы больше подходит для литья сплавов в условиях среднего и низкого давления, чем литье под давлением, особенно в случаях, когда требуется более высокая прочность, лучшая коррозионная стойкость и меньшие припуски на обработку.
2. Какие материалы подходят для литье в постоянные формы ?
Подходящие металлические материалы
Литье в постоянные формы подходит для обработки металлических материалов с низкой температурой плавления и хорошей текучестью, наиболее распространенными из которых являются алюминиевые сплавы, такие как A356, ADC12, A380, ZL101, ZL102 и т. д. Алюминиевые сплавы не только легкие, но и обладают хорошей теплопроводностью и коррозионной стойкостью. Они также могут быстро затвердевать в металлических формах, достигая хорошей плотности и качества поверхности, что делает их наиболее широко используемыми материалами.
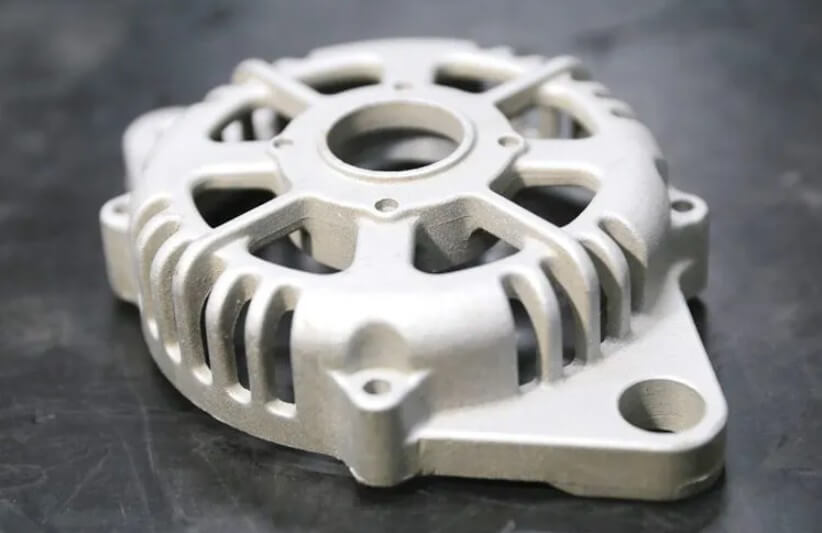
Отливки из алюминиевого сплава
В дополнение к алюминиевым сплавам, магниевые сплавы также очень подходят для литье в постоянные формы , особенно в областях, где требования к весу чрезвычайно чувствительны, таких как аэрокосмическая или автомобильная промышленность высокого класса. Медные сплавы (такие как латунь и бронза) также широко используются в некоторых промышленных компонентах, особенно тех, которые требуют износостойкости и электропроводности. Кроме того, некоторые цинковые сплавы также могут использоваться для литье в постоянные формы , но частота использования меньше.
Неподходящие металлические материалы
Следует отметить, что литье в постоянные формы не подходит для литья металлов с высокой температурой плавления, таких как углеродистая сталь, нержавеющая сталь и жаропрочные сплавы, поскольку эти материалы быстро вызывают термическую усталость формы, сокращают срок ее службы и требуют чрезвычайно строгого контроля процесса.
3. Каковы преимущества и недостатки литье в постоянные формы ?
преимущество
литье в постоянные формы весьма существенны, особенно подходят для изготовления металлических деталей с высокими требованиями к точности, прочности и повторяемости. К его основным преимуществам относятся:
Форму можно использовать повторно, что значительно экономит затраты на пресс-форму при длительном производстве и подходит для средне- и крупносерийного производства.
Точность размеров высокая, допуск можно контролировать в пределах ±0,2 мм, детали имеют хорошую однородность, а объем последующей обработки невелик.
Скорость охлаждения высокая, кристаллическая структура мелкая, прочность отливки высокая, а механические свойства, как правило, лучше, чем у литья в песчаные формы.
Качество поверхности хорошее, обычные отливки могут достигать Ra3.2~Ra6.3 без сложной последующей обработки.
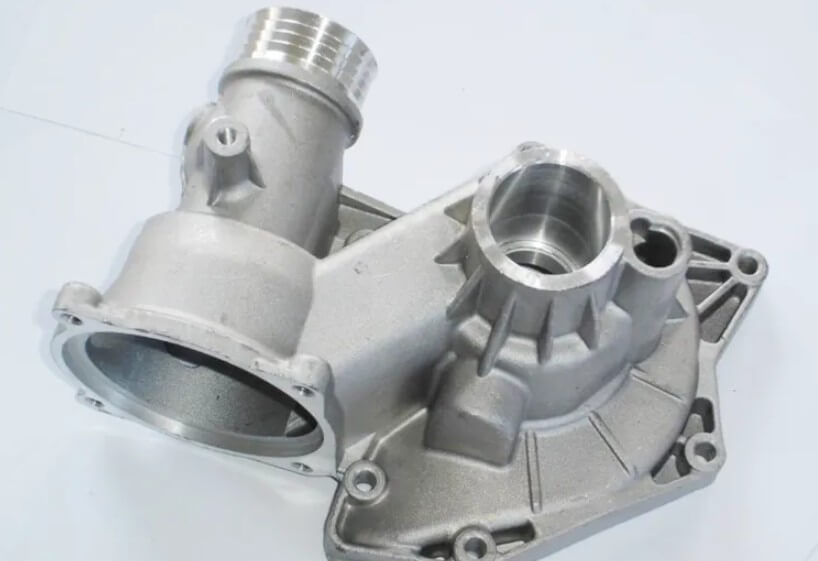
Форма может быть интегрирована с каналами охлаждающей воды, выпускными каналами, устройствами для извлечения стержней и т. д., имеет гибкую структуру и высокую адаптивность.
недостаток
Конечно, этот процесс также имеет определенные ограничения:
Большие первоначальные инвестиции: цикл изготовления пресс-форм длительный, а стоимость высокая, что не подходит для индивидуального изготовления единичных изделий или небольших партий.
Форма детали ограничена: в металлических формах сложно формировать сложные внутренние полости или глубокие отверстия, а устройство для извлечения стержней имеет сложную конструкцию и легко повреждается.
К технологическому процессу предъявляются высокие требования: каждое звено, такое как предварительный нагрев формы, температура заливки, контроль охлаждения, напыление покрытия и т. д., должно строго соответствовать технологическим спецификациям, в противном случае легко могут возникнуть дефекты, такие как поры, холодные швы, усадочные раковины и т. д.
Срок службы формы ограничен: хотя ее можно использовать повторно, форма все равно имеет срок службы из-за термической усталости, который обычно составляет от 5000 до 50 000 раз в зависимости от материала и условий работы.
4. Подробный анализ полного процесса литье в постоянные формы
В процессе литье в постоянные формы , прежде всего, точность формы напрямую определяет, может ли конечный продукт соответствовать требуемым требованиям допуска. Во-вторых, для того, чтобы гарантировать, что литье соответствует установленным стандартам проектирования и точности размеров, весь процесс должен строго выполняться в соответствии с установленными этапами, а также тщательный мониторинг и корректировка должны проводиться на каждом звене. Наконец, в промышленном производстве мы в LVXUN хорошо понимаем , что в промышленном производстве высокий уровень контроля процесса является ключом к обеспечению качества металлических деталей, выполнению технических требований заказчика и адаптации к конкретным сценариям применения.
Изготовление пресс-форм
Перед литьем первым делом необходимо спроектировать и изготовить форму. Обычно форма изготавливается из инструментальной стали, серого чугуна и графита. Выбор материала основывается на том, может ли он сохранять хорошую термическую стабильность и механическую прочность при многократном использовании при высоких температурах.
Форма обычно состоит из двух половин или нескольких секций, которые могут быть оснащены стержнями, вставками, вентиляционными отверстиями и системами охлаждения для достижения более сложной геометрии, полостей и более тонкой толщины стенок при формовании.
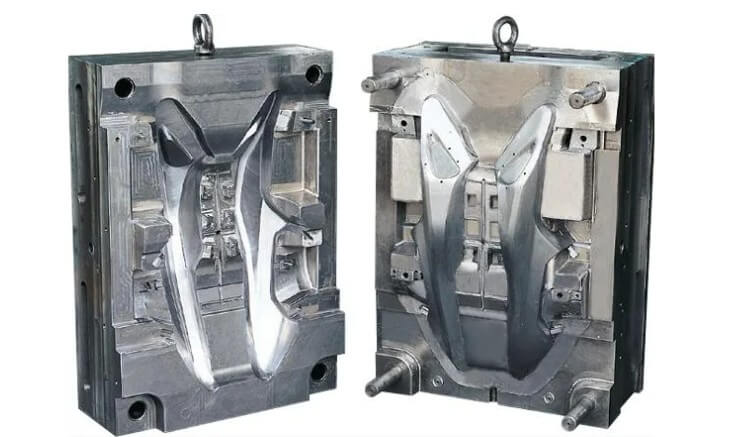
Металлическая форма
Современные литейные предприятия широко используют программное обеспечение для 3D-моделирования САПР и компьютерного моделирования на этапе разработки пресс-форм для прогнозирования путей движения металла, распределения теплового поля и потенциальных дефектов, а также для оптимизации конструкции пресс-формы, литниковой системы и расположения выхлопных труб с целью повышения производительности отливок.
Нагревательная форма
Перед производством необходимо полностью предварительно нагреть форму, чтобы избежать внезапного затвердевания, холодного закрытия или эрозии при попадании расплавленного металла в холодную форму, а также снизить риск растрескивания формы из-за теплового удара. Температура предварительного нагрева обычно устанавливается в соответствии с термическими свойствами выбранного сплава и составляет от 150°C до 300°C. Поверхность формы также должна быть покрыта специальным высокотемпературным стойким покрытием, например, разделительным составом на основе графита или керамики, чтобы обеспечить изоляцию, защиту и плавное извлечение отливки.
Выбор металлического материала
Обычно выбираются цветные металлы с низкой температурой плавления и хорошей текучестью, такие как алюминиевые сплавы, магниевые сплавы, медные сплавы и цинковые сплавы. Алюминиевые сплавы особенно подходят для производства легких автомобилей и авиационных деталей из-за их превосходного соотношения прочности к весу и хороших литейных свойств. В соответствии с требованиями к использованию и эксплуатационным характеристикам отливок также необходимо точно подобрать марку сплава и параметры процесса, такие как температура плавления, температура формы, время заливки и метод охлаждения, чтобы гарантировать, что литые детали имеют хорошие механические свойства, плотность и обрабатываемость.
Заливка расплавленного металла
Заливка является одним из ключевых звеньев во всем процессе литья. Литье в постоянные формы может быть выполнено различными способами, такими как гравитационная заливка, наклонная заливка, заливка под низким давлением или вакуумная заливка. Традиционная гравитационная заливка подходит для деталей с относительно простой структурой. Она проста в эксплуатации, но имеет ограниченную текучесть и заполняющую способность. Технология наклонной или обратно-наклонной заливки может контролировать скорость заполнения металла, уменьшать турбулентность и снижать риск появления включений и пор. В ситуациях, когда внутреннее качество отливки чрезвычайно высокое, например, при производстве деталей для аэрокосмической или медицинской техники, технология вакуумной заливки часто используется для удаления воздуха из полости формы путем применения отрицательного давления. Целью этого является улучшение плотности и целостности отливки.
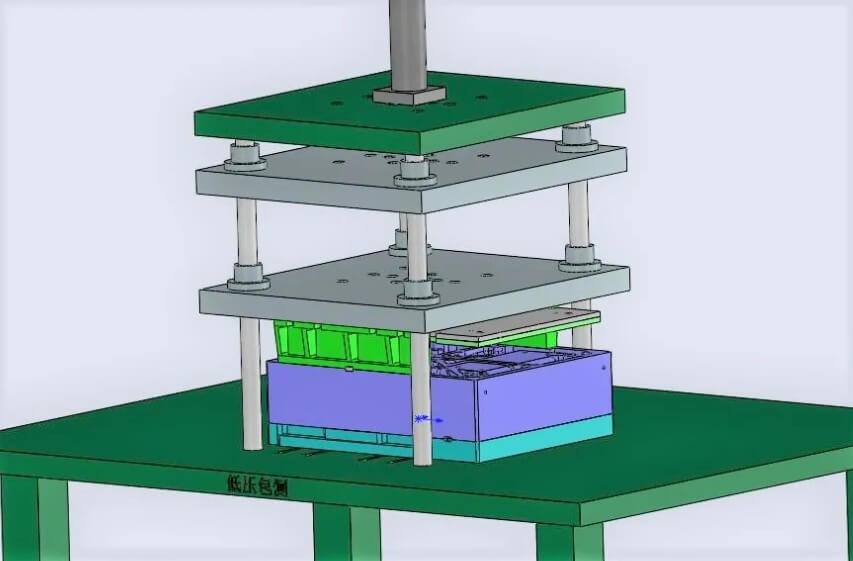
Моделирование литья металла
Охлаждение и затвердевание
Металлический материал постоянной формы обладает высокой теплопроводностью, что позволяет добиться более быстрого охлаждения, помогает формировать мелкие и однородные зерна и повышает прочность и ударную вязкость детали. Для достижения более сложного управления температурой форма часто имеет встроенные каналы охлаждения или использует внешние устройства воздушного охлаждения . Критическая конструкция системы охлаждения влияет не только на эффективность цикла, но и на повторяемость продукта и стоимость обслуживания формы. Тщательно разрабатывая стратегию охлаждения, которая соответствует сплаву и структуре детали, производители могут улучшить качество литья, сократить количество брака и продлить срок службы дорогостоящих постоянных форм.
Снятие и выталкивание деталей
Когда отливка затвердевает, система выталкивания в форме используется для плавного извлечения отливки из полости формы. Система включает в себя выталкивающие штифты, толкающие пластины, гидравлическое выталкивание и т. д., которые обеспечивают целостность деталей, сохраняя при этом повторяемость и эффективность конструкции формы. Чтобы предотвратить растрескивание или прилипание отливки к форме во время извлечения из формы, при проектировании следует учитывать соответствующий угол наклона и обработку поверхности. Для литья LVXUN обычно используется современное литейное оборудование , которое оснащено автоматизированной системой выталкивания для дальнейшего повышения эффективности производства и снижения неопределенности, вызванной ручным вмешательством.
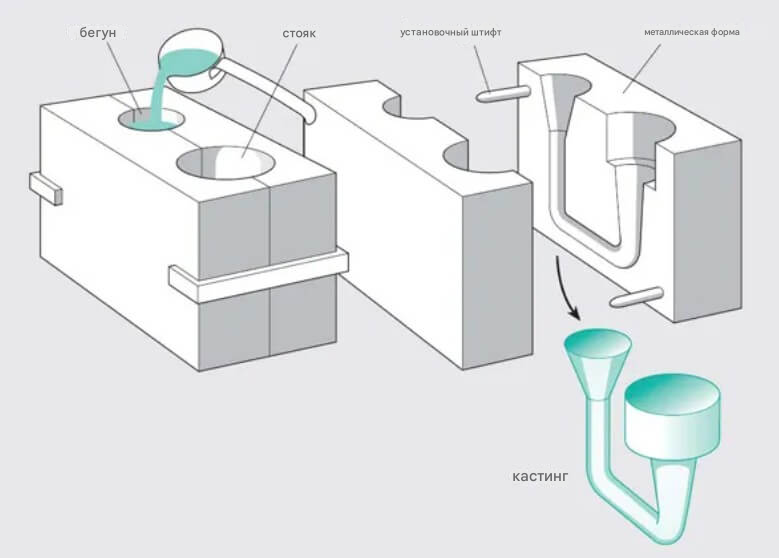
Принципиальная схема процесса литья в постоянные формы
5. Для каких типов деталей или отраслей промышленности подходит литье в постоянные формы ?
Литье в постоянные формы широко используется в промышленных деталях, которые требуют высокой структурной прочности, точности и размерной однородности, и производятся средними и крупными партиями. Ниже приведены несколько типичных отраслей и примеров применения:
Автомобильная промышленность:
Такие как блок двигателя, головка блока цилиндров, корпус водяного насоса, корпус коробки передач, масляный поддон, кронштейн подвески, кронштейн тормоза и т. д. Эти детали обычно выполняют такие функции, как опора давления, рассеивание тепла и амортизация, и должны иметь высокую структурную прочность и хорошую размерную точность. Литье в постоянные формы как раз соответствует этим требованиям.
Аэрокосмическая промышленность:
Такие как соединители сидений, опорные рамы, топливораспределительные трубы и т. д. Эти компоненты имеют чрезвычайно высокие требования к балансу между весом и прочностью. Легкость и высокая прочность алюминиевого сплава полностью отражены посредством литье в постоянные формы .
Электрооборудование и бытовая техника:
Например, корпуса двигателей, торцевые крышки компрессоров, радиаторы, корпуса электронного оборудования и т. д., к которым предъявляются высокие требования по теплоотводу, коррозионной стойкости и внешнему виду.
Гидравлика и промышленное оборудование:
Детали, работающие под давлением, такие как корпуса клапанов, коробки передач, корпуса органов управления и т. д., широко используются в машиностроении, сельскохозяйственной технике и оборудовании промышленной автоматизации.
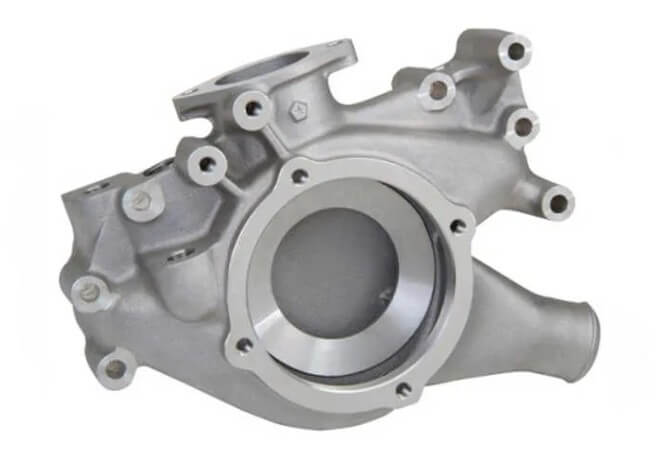
6. В чем разница между литье в постоянные формы и литьем под давлением (литьем под давлением)?
Хотя и при литье в постоянные формы , и при литье под давлением используются металлические формы, между ними имеются существенные различия с точки зрения характера процесса, эксплуатационных характеристик деталей и областей применения:
Различные методы заливки:
Литье в постоянные формы использует естественную гравитацию или заполнение под низким давлением, а скорость заполнения низкая. Подходит для деталей с однородной структурой и небольшим внутренним напряжением. Литье под давлением, с другой стороны, вдавливает расплавленный металл в полость формы под высоким давлением и высокой скоростью, что позволяет производить сложные тонкостенные конструкции, но склонно к образованию пор и накоплению напряжений.
Различия в структуре пресс-форм:
Конструкция литейной формы более сложная и должна выдерживать воздействие высокого давления. Она часто имеет несколько механизмов вытягивания стержней, контуры охлаждающей воды и выхлопные системы; в то время как структура постоянной формы относительно проста и подходит для деталей средней сложности.
Литейные свойства:
Литые изделия, полученные методом постоянного литья, обычно имеют мелкое зерно, мало пор, пригодны для последующей термической обработки и обладают отличными механическими свойствами; в то время как изделия, полученные методом литья под давлением, подвержены образованию пор из-за высокоскоростного заполнения, не подходят для термической обработки типа T6 и обладают несколько меньшей прочностью.
Качество поверхности и эффективность:
Литье под давлением обеспечивает очень хорошее качество поверхности и высокую эффективность производства и подходит для изделий с годовым объемом производства более сотен тысяч штук; литье в постоянные формы имеет меньшую эффективность, но больше подходит для деталей, требующих структурной прочности и комплексных эксплуатационных характеристик.
Подвести итог
Благодаря всестороннему анализу и представлению можно сделать вывод , что литье в постоянные формы является экономически эффективным решением между литьем в песчаные формы и литьем под давлением, особенно подходящим для промышленных металлических деталей среднего объема, высокого спроса и средней сложности.
Возможности кастинга LVXUN
В области литья металлов LVXUN всегда предоставляет клиентам надежные решения, основанные на стабильном управлении процессами и богатом практическом опыте. У нас есть передовые литейные производственные линии, высокоточное обрабатывающее оборудование и профессиональная инженерно-техническая команда, которая может гибко реагировать на различные индивидуальные детали со сложной структурой и высокими требованиями к точности.
Более того, от литья до обработки на станках с ЧПУ и последующей обработки поверхности, мы предоставляем клиентам комплексное обслуживание, гарантируя точность и эффективность каждого звена, а также максимально повышая однородность продукции и эффективность поставок.
Благодаря глубокому пониманию свойств материалов и строгому контролю деталей процесса, LVXUN может не только соответствовать требованиям к поставке и качеству массового производства, но и достигать хорошего баланса в производительности продукта, внешнем виде и контроле затрат. Наши клиенты охватывают множество отраслей промышленности и завоевали широкое признание и долгосрочное сотрудничество.
Выбор LVXUN означает выбор партнера по литейному производству с надежной технологией, быстрым реагированием и надежностью . Мы с нетерпением ждем возможности изучить эффективные и высококачественные производственные решения вместе с вами .
What do you think?
[…] цилиндров двигателя и блок двигателя, как основные компоненты двигателя, имеют много […]
[…] превосходит воображение. Блок цилиндров двигателя и блок двигателя, как основные компоненты двигателя, имеют много […]
[…] используемых способа изготовления алюминиевый блок двигателя, включая технологию литья под низким давлением, […]
[…] двигателя (например, блок двигателя, масляный поддон и т.д.), система трансмиссии (например, […]
[…] вес, высокая прочность требований частей, таких как автомобильный блок двигателя, головка блока цилиндров, ступица колеса, […]
[…] двигателя значительно тяжелее блоков двигателей из алюминиевых сплавов, что увеличивает вес автомобиля, влияет на […]