Low pressure die casting: a high-quality, low-risk process option
In modern industrial manufacturing, casting technology has become one of the core processes for the production of metal parts due to its high efficiency and precise forming capabilities.
Compared with the well-known high pressure die casting, low pressure die casting plays an irreplaceable role in the field of high-end manufacturing with its unique process advantages.
From automobile wheels to aerospace structural parts, low pressure die casting has achieved a leap-forward improvement in casting quality by relying on the core principle of “low-pressure filling and high-pressure shrinkage”. This article will systematically analyze this “hidden champion” of precision manufacturing from the dimensions of technical principles, equipment composition, application scenarios and future trends.
1.The core definition and principle of low pressure die casting: Casting precision in low pressure
(1) What is low pressure die casting?
Low pressure die casting is a casting process in which molten metal is steadily pressed from the bottom to the top of the riser at the bottom of a sealed crucible into the mold cavity through a low-pressure gas (such as compressed air or nitrogen) of 0.01-0.06 MPa, and solidified under pressure. Its core feature is “low-speed filling and continuous pressure maintenance”, which avoids the turbulence defects of traditional gravity casting. It is also different from the high-speed impact of high pressure die casting. It is a “golden mean” between gravity casting and high pressure die casting.
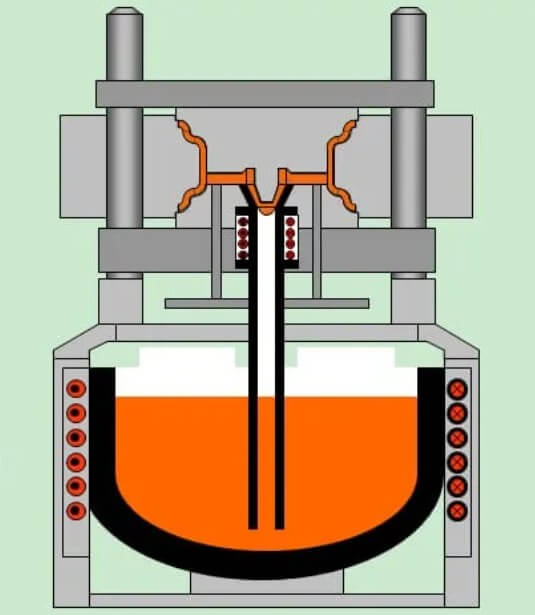
(2) Working principle: “defect-free casting” is achieved in three steps
Step 1: Steady liquid filling. The molten metal flows along the liquid riser at a low speed of 0.1-0.5 m/s under low pressure drive, filling the cavity evenly like “pouring water into a cup”, avoiding splashing and oxidation slag inclusions (the filling speed of traditional gravity casting can reach 5-10 m/s, which is prone to turbulence).
Step 2: Continuous pressure maintenance After the metal liquid fills the cavity, the pressure is maintained for 2-30 minutes (depending on the thickness of the casting) to form “directional solidification”: the metal liquid at the thick wall continuously shrinks to the thin wall through the runner, eliminating shrinkage holes, and making the density of the casting reach more than 98% (close to the level of forgings).
Step 3: Depressurization and demolding After solidification is completed, the pressure is released, and the unsolidified metal liquid in the riser flows back to the crucible to avoid waste of pouring and riser (waste rate <5%). After the mold is opened, high-precision castings can be obtained.
2.Introduction to key equipment for low pressure die casting
The core equipment of low pressure die casting is the carrier for achieving “precise pressure control”, which mainly includes four modules:
(1) Sealed crucible and insulation system
Function: Store molten metal and maintain temperature (about 680-730℃ for aluminum alloy and about 640-680℃ for magnesium alloy). Common materials are heat-resistant alloys or graphite. Some are equipped with electromagnetic stirring devices to even out the melt.
Technical points: Sealing directly affects pressure stability. Minor air leakage will cause filling failure, which requires real-time monitoring through pressure sensors.
(2) Riser and filling system
Core components: The riser is made of refractory material (such as corundum ceramic), with an inner diameter of 50-150 mm and a length designed according to the mold height, taking into account both the flow resistance of the molten metal and the shrinkage compensation efficiency.
Innovation direction: The new “variable cross-section riser” can optimize the filling speed and reduce eddy currents, which is especially suitable for complex structural parts.
(3) Metal mold and temperature control system
Mold material: The mainstream is H13 hot working die steel, with nickel plating or nitriding treatment on the surface to improve wear resistance, and the mold preheating temperature is 150-250℃ (controlled by electric heating or circulating water).
Design key: The cavity must follow the “sequential solidification principle”, with risers set at thick walls and guide grooves set at thin walls to ensure smooth pressure shrinkage compensation channels.
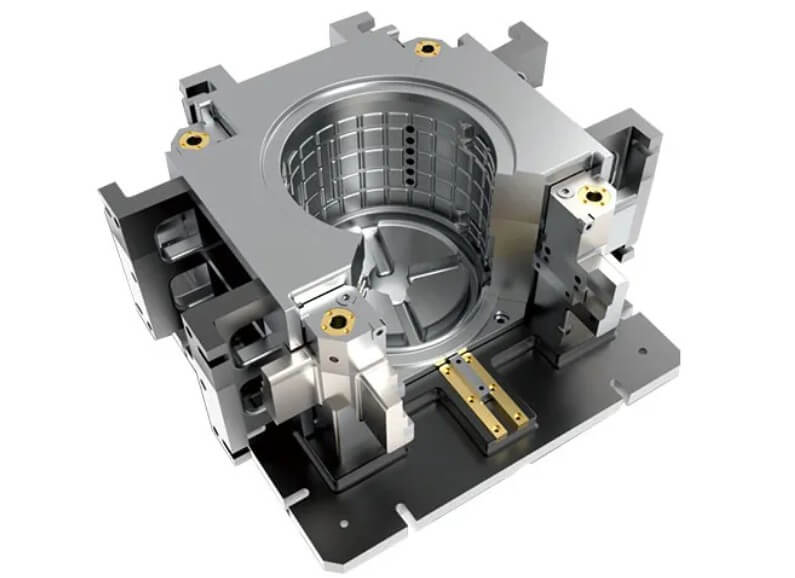
(4) Pressure control system
Core components: including air source (air compressor/nitrogen cylinder), proportional valve, PLC controller, to achieve precise control of the entire process of “pressurization speed – pressure holding pressure – pressure relief timing” (pressure fluctuation needs to be <±0.001 MPa).
Intelligent upgrade: Introduce PID algorithm to automatically adjust the pressure curve, combined with infrared temperature measurement real-time feedback, reduce the scrap rate to less than 1%.
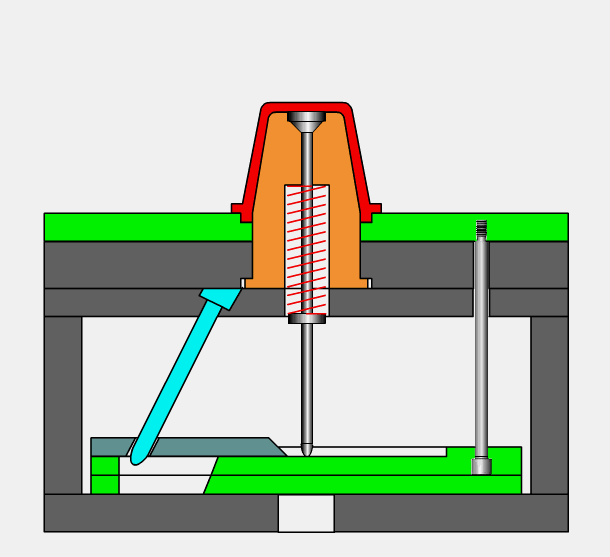
3.Process advantages of low pressure die casting: Why is high-end manufacturing inseparable from low pressure die casting?
(1) Casting quality “rolling grade” advantage
High density: continuous pressure holding and shrinkage compensation eliminate shrinkage holes, tensile strength is 20%-30% higher than gravity casting, fatigue life is increased by 50%, suitable for parts that withstand alternating loads (such as automobile wheels).
Heat treatment compatibility: Due to the low porosity (<0.5%), T6 heat treatment (solid solution + aging) can be performed, and the strength of aluminum alloy castings is increased from 200 MPa to more than 350 MPa.
High dimensional accuracy: The tolerance can reach CT6-7 level (±0.1-0.3 mm), the surface roughness Ra 1.6-3.2, and it can be assembled without machining.
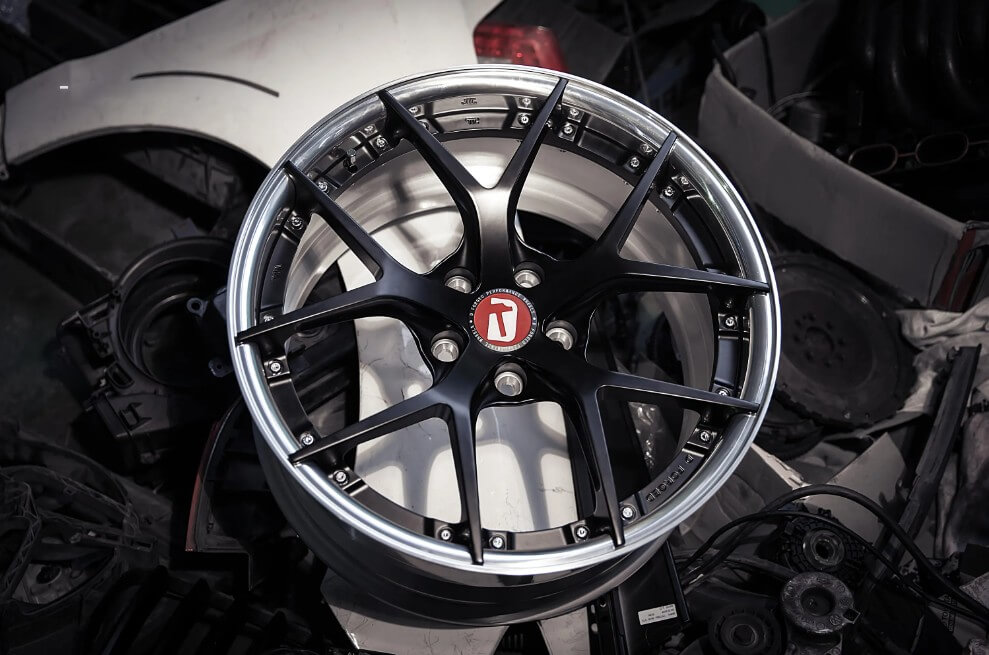
(2) Wide adaptability of materials and structures
Applicable materials: aluminum alloy (accounting for 80%, such as A356, ADC12), magnesium alloy (AZ91D, used for lightweight parts), and even copper alloy and zinc alloy can be formed (high pressure die casting is difficult to achieve).
Structural capabilities: It can produce parts with a wall thickness of 1.5-50 mm, from thin-walled shells (such as laptop magnesium alloy shells) to large thick-walled parts (such as the lower shell of a car battery pack, with a size of more than 1.5 meters), and complex ribs and boss structures can be formed in one go.
(3) Green manufacturing and cost advantages
Material utilization rate: up to 95% or more (the metal of the riser can be recycled, and there is no waste of pouring and riser), which is more environmentally friendly than high pressure die casting (70%-85%) and sand casting (60%-70%).
Mold life: under low-pressure environment, the mold load is small, the thermal fatigue damage is low, and the life of complex molds can reach 300,000-500,000 times (the life of complex molds in high pressure die casting is about 100,000-200,000 times), and the long-term maintenance cost is reduced by 40%.ach 300,000-500,000 times (the life of complex molds in high pressure die casting is about 100,000-200,000 times), and the long-term maintenance cost is reduced by 40%.
4.Typical application scenarios of low pressure die casting: “Quality responsibility” from the automotive industry to aerospace
(1) Automotive industry: dual choice of lightweight and safety
Aluminum alloy wheels: more than 70% of aluminum alloy wheels in the world are made of low pressure die casting because of their high fatigue strength (can withstand 1 million cycles of load) and meet the safety requirements of high-speed driving.
New energy vehicles: battery pack shell (needs to be impact-resistant and leak-proof), motor end cover (needs high thermal conductivity), integrated body structure (such as some parts of the rear floor of Tesla Model Y are made of low-pressure die-casting + heat treatment strengthening).
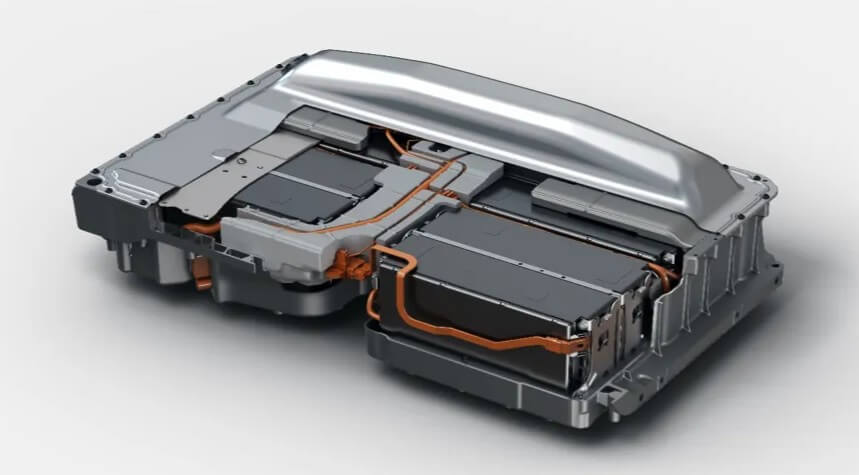
(2) Aerospace: The first choice for performance in harsh environments
Aircraft structural parts: wing ribs, door frames, landing gear brackets, which need to be heat treated with T6 to achieve high strength and corrosion resistance. Low-pressure die-casting is the only casting process that can meet mass production requirements.
Aerospace engine parts: compressor casings and bearing seats, which work in high temperature and high vibration environments. The dense structure of low-pressure die-casting makes its reliability far superior to other casting methods.
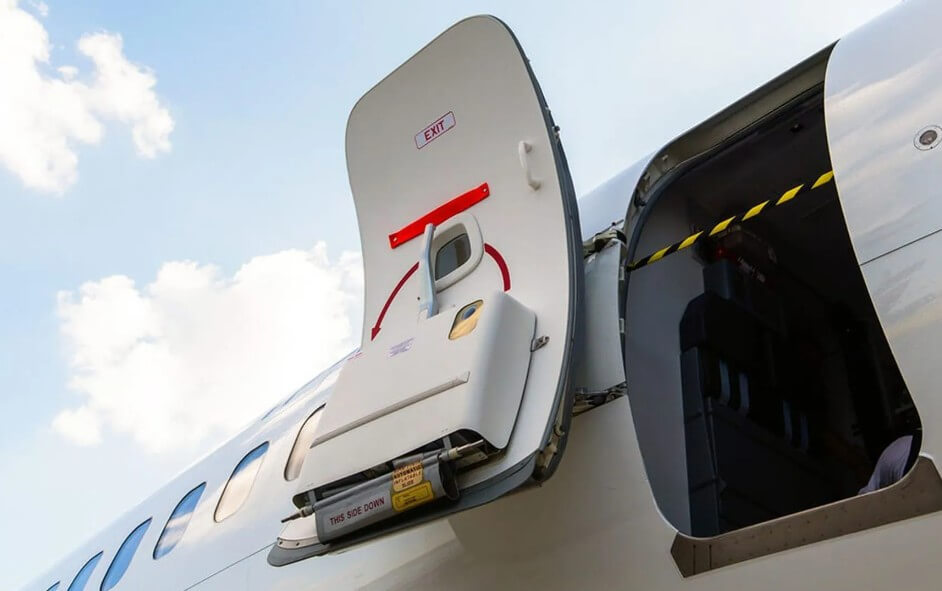
(3) Consumer electronics and high-end equipment
3C products: high-end laptop magnesium alloy shell (wall thickness 1.2 mm, taking into account both lightness and strength), drone racks (needs to be drop-resistant and impact-resistant).
Precision machinery: robot joints (accuracy ±0.05 mm), hydraulic valve bodies (complex internal flow channels, no leakage required), optical lens brackets (high dimensional stability requirements).
5.Current technical bottlenecks and breakthroughs of low pressure die casting
(1) Current challenges
Production efficiency: Single mold cycle 2-10 minutes (high pressure die casting only 10-30 seconds), not suitable for large-scale production of simple parts.
Process sensitivity: Pressure, temperature, and filling speed must be precisely matched. Minor parameter deviations may lead to insufficient pouring or shrinkage (such as a 30% increase in defect rate when the pressure fluctuation is >0.005 MPa).
Dependence on large equipment: The production of ultra-large castings (such as integrated automobile chassis) requires 10,000-ton clamping force equipment, with an initial investment of more than 100 million yuan, which is difficult for small and medium-sized enterprises to afford.
(2) Technological innovation direction
Vacuum low pressure die casting: Vacuum the cavity (pressure <10 kPa) to further reduce pores and enable magnesium alloy castings to be anodized (such as Apple laptop shells).
Semi-solid die casting: Cool the molten metal to a semi-solid state (solid phase ratio 30%-70%) to improve filling stability. It is suitable for high-melting point alloys (such as copper alloys and titanium alloys).
6.How to choose low pressure die casting? Three core decision points
Performance first: If the casting needs heat treatment strengthening, high fatigue strength or harsh environment service (such as aviation, new energy vehicles), low pressure die casting is the only choice.
Batch and cost: For small and medium batches (<30,000 pieces) or large and complex parts (such as single piece weight >50 kg), low pressure die casting has significant advantages in mold cost and material utilization.
Structural complexity: For parts with deep cavities, multiple ribs, and uneven thickness, the stable filling and shrinkage capacity of low pressure die casting far exceeds gravity casting, and the cost is lower than precision forging.
7.Conclusion: Low pressure die casting opens a new dimension of high-end manufacturing
From “usable” to “easy to use”, low pressure die casting has achieved a leap from casting to “precision casting” by virtue of its exquisite control of “pressure”. Under the trend of “lightweight” of new energy vehicles, “high performance” of aerospace, and “precision” of consumer electronics, this precise and strong process is ushering in a golden period of development.
LVXUN has extensive manufacturing experience in pressure casting, and its products are widely used in a variety of industries such as aerospace, automobiles, and consumer electronics. Welcome to visit our service page to learn what processes we can do. If you have any questions about the process, please feel free to consult us!
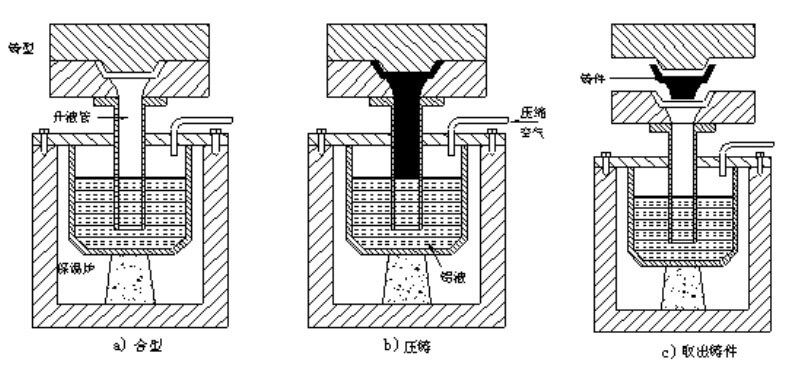
Answers to common questions about low pressure die casting:
What is low pressure die casting? How is it different from high pressure die casting?
There are two types of pressure casting processes: low pressure and high pressure die casting
Low pressure die casting is a casting process in which molten metal is controlled by low air pressure so that it slowly fills the metal mold cavity from bottom to top from the insulation furnace. High pressure die casting is a process in which metal is injected into the mold cavity from top to bottom at high speed through high pressure of hundreds or even thousands of kilopascals.
The difference between the two can be summarized in one sentence: low pressure die casting: low pressure, bottom-up, slow; high pressure die casting: high pressure, top-down, high speed. It is precisely because of their different process principles and process flows that their advantages and the parts they are good at producing are also different.
Compared with high pressure die casting, low pressure die casting has a slower filling speed, a smoother flow of molten metal, and is not prone to defects such as flash and pores. It is suitable for aluminum alloy parts with high requirements for density and strength. The advantage of high pressure die casting is that it has extremely high production efficiency and is suitable for mass production, but its high-speed impact will cause internal defects such as pores, and the mold wear is relatively fast.
In general, low pressure die casting emphasizes the controllability of the process and the high quality of castings. It is suitable for medium and large parts with complex structures, high precision requirements or subsequent heat treatment. High pressure die casting is more inclined to high-efficiency, low-cost mass industrial production.
What metal materials are suitable for low pressure die casting?
Low pressure die casting is most commonly used for the forming of aluminum alloys, especially in automobiles, aviation, industrial machinery and other occasions with high requirements for structural strength and weight. It is widely used. Common aluminum alloys include Al-Si series, Al-Mg series, etc. These materials have good fluidity and thermal cracking resistance, and are suitable for slower filling processes.
In addition to aluminum alloys, low pressure die casting is also suitable for some magnesium alloys and copper alloys, but aluminum alloys are still the mainstream. In addition, considering the mold life and economy, it is generally not used for metals with too high melting points, such as steel materials.
What is the cost of low pressure die casting? Will it be more expensive than high pressure die casting?
Compared with high pressure die casting, the equipment structure of low pressure die casting is simpler and does not require a huge injection system, so the initial equipment investment is slightly lower. In addition, in terms of molds, the molds of low pressure die casting are subjected to less pressure during use, so the life is generally longer and the maintenance cost is lower.
However, the production efficiency of low pressure die casting is lower than that of high pressure die casting, and the molding cycle is longer. Therefore, in mass production scenarios, the unit cost of each product will be higher than that of high pressure die casting. However, in small or medium-volume customized production, because the castings produced by low-pressure casting are of good quality, the overall subsequent processing cost is reduced.
In other words, if your project focuses on precision, strength, airtightness and reliability, low pressure die casting is very cost-effective. If you pursue the ultimate output and unit cost compression, high pressure die casting has more advantages. The choice of which method needs to be weighed according to the specific project scale and product requirements.After reading the above, if you already know what process to choose to produce your parts, you can get a quote from us online;if you still have doubts, you are welcome to communicate with us at any time, and we will provide you with professional advice.
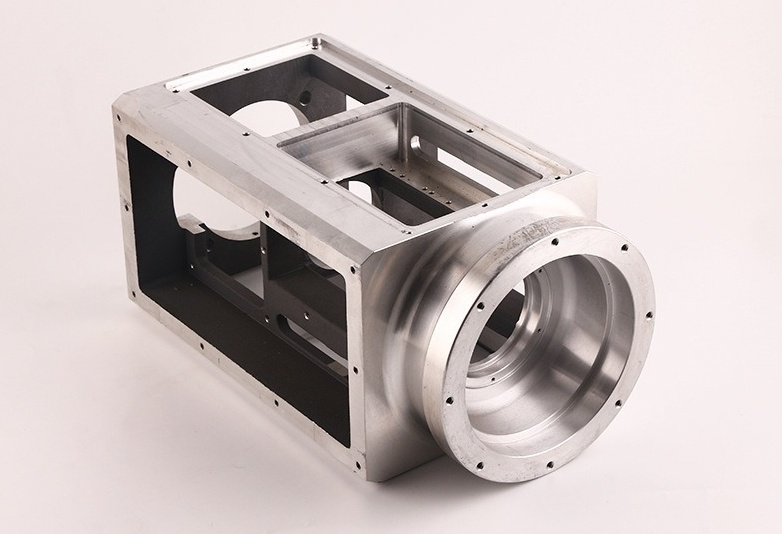
Is low pressure casting suitable for customization or small batch production?
After the introduction of the above content, I believe you already have the answer to this question in your mind. Yes, low-pressure die casting is particularly suitable for customization and small batch production, which is one of its important advantages over high pressure die casting.
If your product requires rapid iteration of design or needs to provide customized functional parts, then low-pressure die casting just meets this demand.
In summary, whether it is a small batch of multiple varieties or customized parts manufacturing, low-pressure die casting is a high-quality, low-risk, and highly adaptable process choice.